Industrial roofing and roof repairs differ significantly from the residential roofing sector. This article covers everything you need to know about industrial roofing, including the materials they are made of, repair and replacement options, weatherproofing techniques, and the best materials to use.
What is an industrial roof?
An industrial roof refers to the top covering of your business premises, which can either be flat or sloped. There are several types of industrial roofs, each with distinct characteristics and benefits. Some examples include Metal roofs, Modified Bitumen roofs, Built-up roofs, TPO roofs, EPDM roofs, and PVC roofs.
Common repair problems
Industrial roofs are susceptible to various repair issues, including:
- Roof leaks and water damage: These issues can be caused by standing water, clogged drains, or damaged membranes.
- Punctures and Tears: Foot traffic and debris can create openings, leading to more significant damage.
- Roof shrinking and blistering: Temperature changes can cause cracks and bubbles, weakening the roof.
- Roof flashing: Damaged flashing allows water infiltration, leading to additional problems.
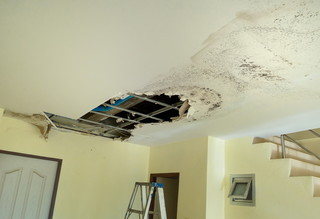
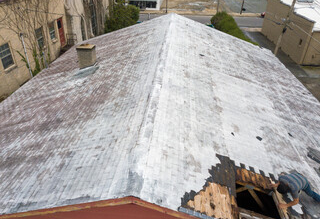
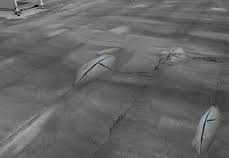
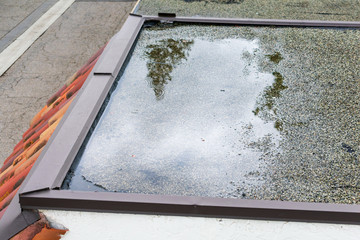
These common repair problems can result in water damage, energy inefficiency, safety hazards, and more. To maintain your roof’s condition and address any damage, regular roof inspections are essential.
Having regular inspections can:
- Prevent expensive damages.
- Extend the roof’s lifespan.
- Reduce energy consumption and costs.
Protective measures and preventing future damages
Whether you have an existing roof or plan to install a new one, there are various ways to protect and prevent future damages. Some of these measures include:
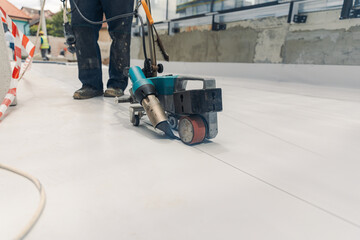
Roof coatings and waterproofing:
Installing a PVC membrane over the roof can increase durability and longevity, acting as a barrier between the building and the elements, preventing roof damage.
Roof sealant:
This special fluid applied across the membrane of your roofing system prolongs its service life by protecting it from leaks, sun damage, and ponding water.
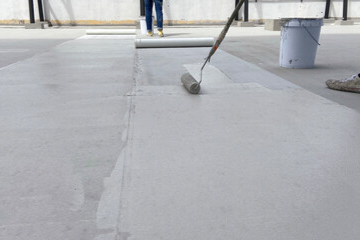
When should you replace your roof?
If repairs to your roof prove inadequate, replacement may be necessary. Here are some signs to look out for when considering a roof replacement:
- Water infiltration: Frequent water infiltration or a history of leaks may indicate the need for a replacement. Even if the roof’s membrane appears adequate, moisture might be trapped underneath, leading to poor insulation and roof deterioration.
- Roof Membranes: While assessing the entire roof membrane, watch for signs of uplift, tears, rips, or damage. If you notice the membrane lifting or peeling away from the roof, replacement is necessary.
- Extreme temperatures: Unusual temperature fluctuations inside your building could signal roof damage. Energy efficiency is crucial for reducing costs in industrial buildings, and a damaged roof could lead to high energy expenses. Replacing the roof to comply with efficiency regulations can help address this issue.
Roof repairs and replacements are essential to maintaining a safe working environment and complying with local roof regulations. If you have experienced any of the above issues, it may be a sign that your roof requires repair or replacement.
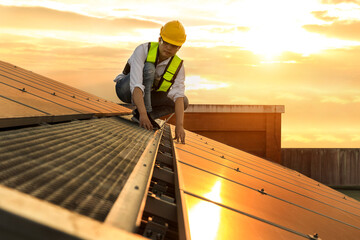
Our process:
We begin by evaluating the condition of your roof, enabling us to identify any issues and devise a tailored solution. Depending on the assessment, we may recommend roof repairs, preventive measures, partial replacement, or full replacement. After finalising the roof plan, we proceed with the necessary work. Following the replacement or repair, we highly recommend scheduling a roof inspection every six months. With regular inspections and maintenance, an industrial roof can typically endure for 10-30 years.
If you require roof repairs or any roof related services, contact us today to discuss how we can help you.